HDPE pipe in power plant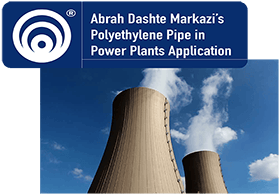
HDPE PIPE in Power Plant
HDPE pipe is the best choice for a variety of energy industry applications. The most critical part of a power generation plant is Cooling water pipe systems if Cooling water pipe systems fail,the whole plant may shut down. HDPE is an ideal candidate for coal power plant applications. HDPE has a high wear resistance when compared with competing products such as steel. In fact, laboratory tests have proven that HDPE can last up to three to five times longer than normal or fine-grained steel pipe
Polyethylene Raised Temperature (PE-RT) Pipe in Power Plant
Abrah Dashte Markazi Company manufacturer Polyethylene Raised Temperature (PE-RT) Pipes base on latest specification With type 1 and type 2 PE-RT material according to DIN 16833, ASTM F2769 - 16, ISO 15494, ISO 24033, EN 15632-2. Abrah Dashte Markazi's Polyethylene Raised Temperature (PE-RT) Pipe provides the practical solution when reaching the higher capacity of polyethylene pipes working Temperature is required PE-RT is suitable for use in all hot water pipe applications.
Abrah Dashte Markazi's Polyethylene Raised Temperature (PE-RT) Pipe for cooling water systems in Power plants based on these pipes can be connected via heat fusion welding or by the use of mechanical fittings. Furthermore, Abrah Dashte Markazi's Polyethylene Raised Temperature (PE-RT) Pipe can be used in industrial applications, where its temperature resistance may limit traditional Polyethylene and metallic materials often suffer from corrosion. The excellent weldability of Abrah Dashte Markazi Company's Polyethylene Raised Temperature (PE-RT) Pipe provides various opportunities to connect even larger dimension pipes in industrial applications
HDPE pipe's qualification For energy industry applications
The use of HDPE in the power plane industry puts a huge spotlight on the unmatched properties of the piping material to provide a safe and cost-effective solution. On 21 July 2009, the Nuclear Energy Institute recognized the use of HDPE pipe with a Top Industry Practice award
This move to HDPE piping systems should be a sign for other utilities to join the fold
It’s no surprise the Power plane facilities would turn to HDPE for both non-safety and safety-related applications. Solid-wall HDPE provides a durable, corrosion-free, leak-free pipeline solution
HDPE Power Plants pipe's Advantages
HDPE has emerged as a reliable and sustainable replacement for steel pipe primarily due to :
-
HDPE pipe is leak-free when produced properly, even at joints, which can be as strong and leak-free as the pipe itself through the use of the heat fusion joining technique.
-
HDPE is corrosion and chemical resistant: It does not rust, rot, pit, corrode, tuberculate, or support biological growth.
-
HDPE offers seismic resistance, in that it can safely accommodate repetitive pressure surges above its static pressure rating and is well suited for seismic loading due to its natural flexibility.
-
HDPE is easier and more cost-efficient to install than carbon steel.
The build-up inside steel pipe reduces not only the C-factor but also the inside diameter
HDPE pipe has the advantage over the metal pipe in total life cycle costs including material, installation, maintenance, and replacement costs. With these outstanding performance attributes, HDPE pipe has been used in power plants over the last 15 years to transport cooling water pipe for non-safety-related applications. In November 2008, Ameren’s Callaway Nuclear Power Plant completed the installation of a 36″ HDPE cooling water pipe system