Polyethylene PIPE advantage
Polyethylene is the most chemically inert (is not chemically reactive) of all commodity plastics raw materials ( polyethylene, polypropylene, polystyrene, polyvinyl chloride, polymethyl methacrylate, and more ) and Polyethylene is chemical and corrosion resistant
Polyethylene Pipe advantage: Flexibility
Polyethylene Due to its flexibility sets apart from other pipe types. it reduces fitting and installation Costs. The polyethylene pipe industry estimates a service life for HDPE pipe to conservatively be 50-100 years. This relates to savings in replacement costs for generations to come
Polyethylene Pipe advantage: Heat Fused joint & Leake free
Polyethylene PIPE can be heat fused to form a joint that is stronger than the pipe itself and is leak-free. Polyethylene PIPE has a mirror-smooth inside surface and because of that Polyethylene PIPE have minimum flow head loss Polyethylene is about one-eighth the density of steel, it does not require the use of heavy lifting equipment for installation
The combination of flexibility and leak-free joints allow for unique and cost-effective types of installation methods that the rigid PVC and Ductile Iron pipes can't use with bell and spigot connection. These cost-effective types of installation methods are Horizontal Directional Drilling (Long lengths of Polyethylene are welded together and then installed under roads, creeks, rivers, etc by a Horizontal Directional Drill (HDD)), Pipe Bursting, Sliplining, Plow and Plant, Submerged or Floating Pipe
Polyethylene Due to its non-metallic nature, the material used is totally resistant to all forms of metallic corrosion. Aggressive water resulting from high sulfate soils and low hardness water will not attack PE pipes.
Abrah Dashte Markazi's pipes are therefore resistant to a wide range of industrial waters and chemicals and offer an advantage in long-term systems life and manufacture costs.
Polyethylene Pipe advantage: smooth inside surface 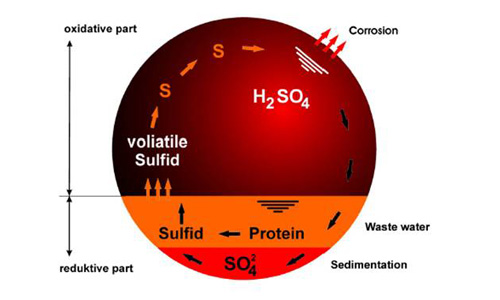
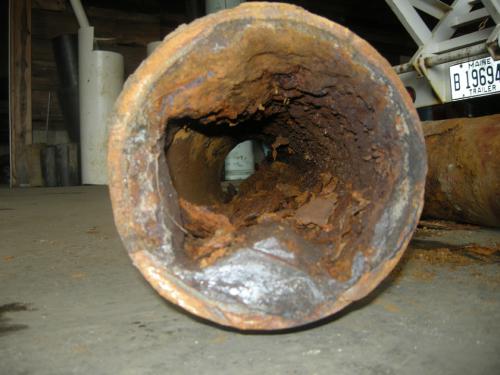
Because of their mirror-smooth inside surface, Polyethylene PIPE has minimum flow head loss. There is also no buildup of inside deposits, a particular advantage in the construction of sewerage systems.
This gives Polyethylene PIPE a significant long-term strength advantage over concrete and metal pipes. Polyethylene pipes have demonstrated, through testing and actual usage, that they meet and even exceed life service requirements for both pressure and drainage applications. The service life of 70+ years is projected where Polyethylene is specified. For years, engineers all over the world have specified Polyethylene PIPE
The comparative figures indicated below, show that old Polyethylene PIPE in water systems continue to have a very low coefficient of resistance ‘n’.
|
‘n’ New Pipe |
‘n’ Old Pipe |
Polyethylene |
0.008 |
0.008 |
Steel |
0.012 |
0.013 |
Cast Iron |
0.013 |
0.015 |
Ductile Iron |
0.012 |
0.014 |
Applicable Standards
Abrah Dashte Markazi produces Polyethylene PIPEs according to the specifications requested by the client. Our product portfolio consists of pipes made according to the following standards:
Water:
DIN 8074 - 8075
ISIRI 14427
ISO 4427
EN 12201-2
Gas:
ISO4437
EN 1555-2
Cutting
The pipe should be cut square. A simple method of cutting pipes square is to wrap newspaper or similar sheet paper around the pipe with no overlap of the edges. Mark line around the pipe (felt pen is ideal). Cut to line with a fine-toothed saw.
Storage
Storage areas for pipes should be clean. Point loading (by gravels and/or rocks) should be avoided at all times. The recommendation for the permitted stacking height for PE pipes not stored on pallets is 1 m. Pipes should be stacked in layers. The area where the pipe is stored should provide as much protection as possible. Pipes should be completely protected from the effects of oil, solvents, and other chemical substances during the storage period. The influence of weather on stored pipes should be kept to a minimum. If the pipes are stored in the open (construction sites), then they should be covered with black sheeting to protect them from the influence of weather (for example, UV rays). Moreover, one-sided heat exposure caused by sunshine can lead to deformations in the pipes. The maximum permitted storage periods should be adhered to (for example, DVGW) Transport Vehicles for transporting pipes should be selected in such a way that the pipes lie completely flat on the floor of the vehicle. Sagging is to be prevented. Impacts are to be avoided. To protect the pipes from damage, please check the loading area for metals and rocks before loading. Pipes should be loaded and unloaded with extreme caution and care
Polyethylene Pipe advantage: industrial Class Pipe
FM Approved piping
Underground piping meets or exceeds operating temperatures and pressures
Cooling Water Applications:
Polyethylene PIPE is an excellent insulator, with minimal heat transfer. Copper transfers heat 2700 times more than Polyethylene.
Polyethylene does not become brittle at 32 deg. F
Polyethylene does not leak, it is seamlessly fused
Polyethylene does not corrode
Instrument Air
Fire-Water
Steam Condensate and Blow Down
Raw Water
Process Water
Withstands freezing water better than traditional metal piping
Systems maintain high fluid flow properties throughout their service life due to excellent chemical and abrasion resistance
The pipe is available in coils through 6" for multiple applications
Is weather resistant:
Carbon black is added to HDPE to provide UV protection
Frozen water will not crack or break Polyethylene PIPE
Is durable:
Withstands fatigue and surges
Safer due to operating pressure capabilities
Butt fused joints eliminate the need for thrust blocks
Delivers long term economy, value, and dependability
• Butt fusion joining of Polyethylene PIPE produces a leak-free joint.
• No gaskets or hardware required.
• The butt fusion weld is as strong as the pipe itself.
• Electrofusion joining produces leak-free joints in confined spaces.
• Smoother ID than steel, cast iron, ductile iron, or concrete pipe.
• Smaller pipes can carry the equivalent flow.
• "Non-stick" inner surface and corrosion resistance preserve excellent hydraulic characteristics for pipe service life.
• Produced in straight lengths and coils.
• Material about 1/8 density of steel.
• Excellent for use in shifting soils or seismically active areas.
• Reduced effects of freezing.
• Available in long lengths on coils & reels.
• Pipe can be bent to accommodate terrain - reduces the need for fittings.
• Flexibility allows easy installation by horizontal directional drilling.
• Flexibility eases installation on slip lining projects.
• Lightweight reduces equipment requirements for handling.
• More resistant to acids, bases, and salts than most other pipe materials.
• Does not rust, rot, corrode, tuberculate, or support biological growth.
• Requires no special coastings nor cathodic protection.
• Excellent abrasion resistance.
• Resists external loads.
• Resists vibrations.
• Resists pressure surges.
• Tolerates handling and bending in severely cold weather.
• Tough.
• Impact resistant